Crankshafts are hardened at the pin, journal, and flange portions. The pin portion is arranged eccentrically with respect to the central axis in order to convert reciprocating motion into rotary motion. DKK’s hardening equipment features a mechanism that allows the coil to follow the eccentricity of the pin portion, ensuring reliable hardening of all parts. We can also provide both R hardening and flat hardening according to your needs.
Front-In Front-Out Method
This is a method in which workpieces are fed in at the front of the machine, processed at the pin, journal, and flange portions, and discharged at the front of the machine as well. This method can be used for both small and large workpieces, ranging from motorcycle to ship parts.
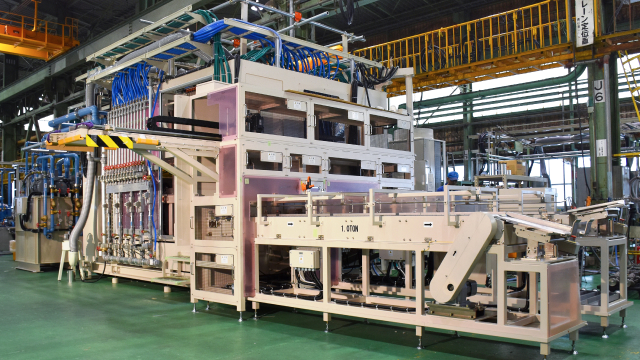
Horizontal Transfer Method
This is a method in which workpieces are fed in from one side, processed at the pin portion stage, and then at the journal/flange portion stage, and discharged at the opposite side of the machine. Workpieces can be placed horizontally or vertically. This method can be used for both small and large workpieces, ranging from motorcycle to ship parts.
Turntable Method
This is a method in which workpieces are transported using a turntable. Since each stage of the processing is centered around the circular table, this method saves space compared to the lift-and-carry method (about 40% less space than our conventional method). This method is suited to comparatively smaller workpieces, such as parts for motorcycles and automobiles.
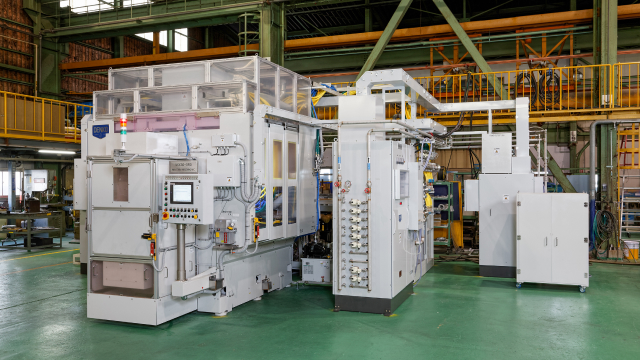
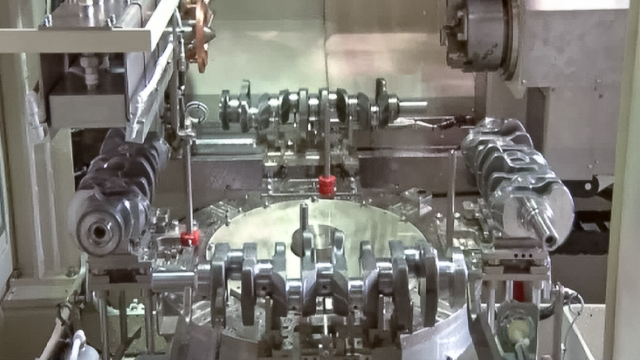
What are Crankshafts?
The crankshaft is an essential part of an engine which converts the reciprocating motion of the pistons in the engine combustion chambers into rotary motion. The crankshaft also plays a critical role in consolidating the energy of multiple pistons.
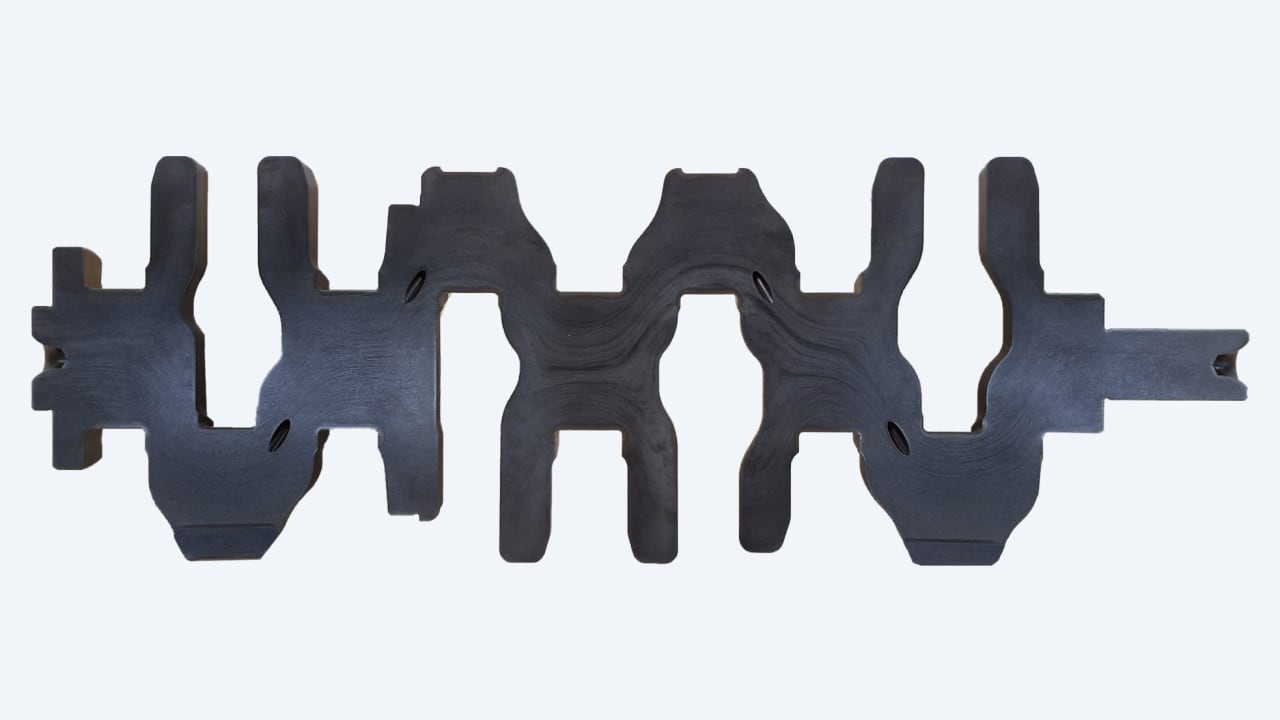